Final Selected Glove Design
- saloni mistry
- Nov 27, 2022
- 4 min read
Over the last two weeks, Team JAMS has selected a final design, received quotes from two 3D printing vendors who informed us they were able to print using our desired material (PEEK), and began analysis for flow rate, torque, glove strain, and ergonomics. The team was running behind, so the final design selection was accelerated to catch up with running analysis on the selected design. Out of the three designs created in the prior work period, the team decided to select the Notch and Groove Mechanism shown below.
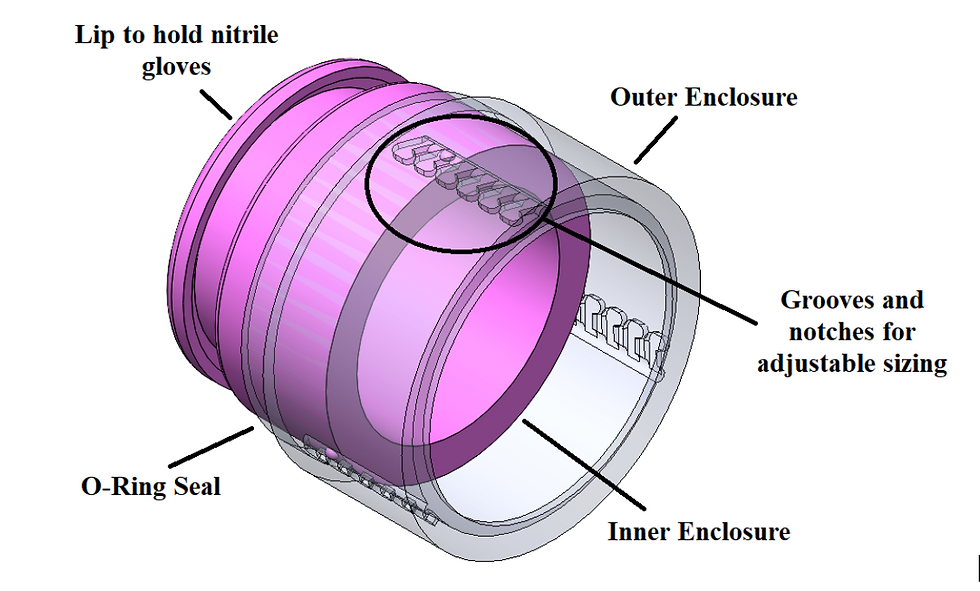
The Notch and Groove Mechanism was selected for its lack of small, mechanical components. This design has much fewer modes of failure since it does not include springs and it has large features relative to the other designs, making it easier to machine. Also, this device can be made entirely of plastic and has a clearer process for fabrication and assembling. This device is similar to the locking wrist wring that is used on the MSG, pictured below. The similar design is advantageous when proposing the final design to NASA with convenient and easily understood integration.
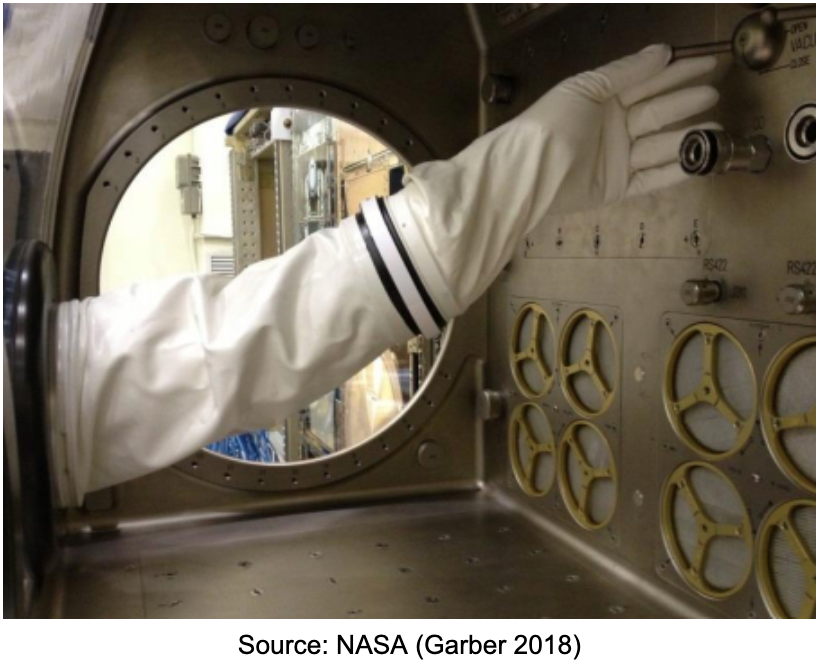
One of the major advantages to the Notch and Groove Mechanism is the lack of radial pressure required to tension the gloves, meaning our radial pressure goal is automatically met and there is no need for analysis regarding the radial pressure from the device onto the wrist.
O-Ring Flow Rate Analysis:
For the design chosen as the final design concept. A seal will be placed between both components of the concept to ensure an airtight seal between the outside environment and the LSG’s slight vacuum. The seal chosen and its cross section dimensions are pictured below:

The shape of this seal will accommodate both forward and backward translation of the two components of the device against each other while being secured in a channel spanning the inside circumference of the outer shell of the device. To verify this seal will function in limiting airflow to the design specification of 10 l/m, Team JAMS is implementing O-Ring Flow Rate analysis researched by NASA. The equation for this flow rate (L) is as follows:

Per our design:
F (Permeability rate of the gas through thermoplastic elastomer at room temp) = 1.4896 * 10^-10 cc cm/cm2 sec bar
D (Inside diameter of the O-Ring) = 5.9055 in
P (Pressure differential across the seal) = 3 psi
Q (Factor based on percent compression of 20% and lubrication) = 0.7
S (Percent compression) = 0.2
L = 8.2761 * 10^-10 cc/sec = 4.966 * 10^-11 l/m
The permeability rate was found via a research paper on thermoplastic elastomers. The pressure differential was estimated based on atmospheric pressure being 0 psi and an absolute vacuum being 14.7 psi all while the LSG is under a slight vacuum internally. Considering the expected airflow of the device is significantly below the design specification, we considered the device a success in this area.
Rough Strain Analysis:
Biological research in the LSG means that ensuring that gloves do not break or deform permanently is essential for the safety of the users, as breakage means that the user will be potentially exposed to working materials, and deformation will reduce the dexterity of the user’s work environment. Because of this, the team has also decided to allocate focus on determining how much work is allowed on the gloves before they break or deform. This is planned to be determined through a strain gauge. However, as of right now, a rough strain analysis has been performed for the purpose of understanding how much the material can stretch, by working with Young’s Modulus, E, for a single axis of the glove material, which is given by the following formula:

where
E is Young’s Modulus
σ is tensile stress
Ɛ is strain
F is the force exerted on an object under tension
A is the cross-sectional area
ΔL is the change in length
L0 is the original length of the object
Young’s Modulus, E is found to be about 4 MPa. With the tensile strength, σ being 15 MPa, and the percent elongation, Ɛ being 350%, the stress and strain from the formula for Young’s Modulus serves as a rough estimate of the amount of force the gloves can experience from arm extension without breaking or deforming.
Torque Analysis:
For our locking mechanism to work reliably, we needed to conduct a force analysis on the enclosure. The forces applied to the mechanism would result in a nominal torque that gives rise to shear stress on the material. The materials we are considering are PEEK or ABS, with a maximum shear stresses of 0.5 MPa and 0.3 MPa respectively (Kruse Training). Although humans typically use a grip strength of 70 N for daily activities, the mean maximum grip strength of 596 N was used for this torque analysis to ensure the functionality of the prototype under extreme conditions (Stokes). The following calculations confirmed a shear stress of around 0.065 MPa, well under the maximum allowable shear stress for the plastics. Even under extreme conditions and forces, our device will safely function as intended

Dr. Holley Love, an instructional associate professor of the mechanical engineering department at University of Houston, advised the team to explore the ergonomics of the design as well as the torque and strain gage analysis, in order to ensure that the design is fulfilling its purpose. As far as the limitations of this design goes, this design will be sort of a loose fitting device which combines both the sleeve and the gloves. Due to this easy-fitting mechanism, there are several ergonomic factors that need to be explored. The Team is currently trying to find a middle-ground between a snug-fit and dexterity.
Over the winter break, Team JAMS will be conducting thorough analysis on the design prior to preparing a prototype. This analysis will consist of making a simpler prototype using simple ring-like objects and performing experimental analysis to check the limitations and flaws that need to be addressed before manufacturing a prototype. Once this design analysis meets all the goals and specifications, Team JAMS will start prototyping the design; however, in the case of any present flaws, then the team will have to confront those issues and try to modify the design accordingly. The team's overall goal for the winter break is to start the prototyping process so that a device is available to test.
Comments