Removed from LSG Schedule, New Validation Plan
- Andrew Tran
- Mar 25, 2023
- 4 min read
Originally, Team JAMS was scheduled to perform validation tests at JSC on the LSG mock up. On March 23rd, we were informed that we were removed from the schedule because of Axiom Mission 2 training and an APEX PV which slipped into our timeslots. In order to validate our final glove mechanism we must build an environment which simulates the primary components of the LSG, a negative pressure workspace with a slight vacuum around 20 cmHg and a glove port. Although we have leeway in our Gantt Chart, this setback may set us back up to 2 weeks accounting for possible errors when fabricating our own LSG environment.
We purchased an aquarium Thursday evening and created a slight vacuum which subsequently imploded as shown below. This weekend we will be rebuilding the crude LSG using plywood and a pressure release valve to achieve a more desirable slight vacuum. The dimensions of our LSG will be approximately 24” x 24” x 24” which is much smaller compared to the actual LSG dimensions of 26” x 36” x 24” but should achieve fairly similar results while saving on costs and allowing us to quickly build and catch up. The top of the wooden glovebox will have a transparent polycarbonate lid with our glove port and pressure gauge. Our validations will be tested using the same procedure, but the results will be less conclusive than tests at the accurate LSG mock up, and any discrepancies between our model and the LSG must be explicit in these final results.

The final glove and sleeve assembly (pictured below) includes a glove mechanism with an inner and outer enclosure 3D printed from PLA. This glove mechanism is attached to a sandblast neoprene sleeve which is connected to a port where users will insert their arms. A glove is clamped to the inner enclosure using an adjustable worm gear with a wing socket.

The Glove Mechanism is a hollow cylinder that can be evacuated by pulling the hands directly out through the glove ports. Evacuation is intuitive and fast with the design implementation. The Glove Mechanism is adjustable and has 5 size settings that can be achieved by twisting the inner enclosure, extending it to the desired length, and twisting it back. This adjustability is somewhat slow and not as intuitive as our original intentions, but the sizing only needs to be selected once so setup time is a small cost to pay. The adjustability coupled with the 3 standard glove sizes provides the user with a more reliable way of keeping the gloves tight and comfortable when compared to what we experienced on the LSG tour. The current method of adjusting the enclosures is not obvious to the user, so there has been a decision to create the final product with a guide for adjustment on the outside of the device, identical to that inside the outer enclosure, as seen below.
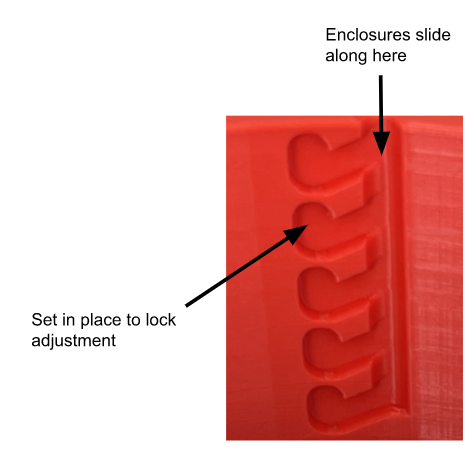
The final glove mechanism has an inner circumference of 30 cm which is above our specification of 25 cm minimum, allowing for users to slip their hands in and out of the mechanism easily. Our design has a predicted evacuation time of less than 2 seconds which is significantly below the team’s validation time of 10 seconds. Due to the NASA setback, the team is behind on the validation data. Once the mock glovebox is made, the team should be able to continue performing the validation procedures with the same methods.
The device is working towards a high level of expected performance when looking at the original goal of the project. The function of the design is very straightforward for the user, and it seems that it will be able to serve its purpose in the LSG. The design analysis has yielded very good numbers compared to the validation goals. One major concern stems from the newfound requirement of having to assemble a crude glovebox for validation. Because the glovebox is being designed in short notice, this may yield different validation results from the intended validation results had the testing occurred at JSC - in turn, possibly deeming the project a failure. Given that it does result in failure, there will be much less time to perform appropriate changes to the design compared to if the team had access to the LSG at JSC.
A majority of the remaining work on the project is to finish developing and tuning a testing environment comparable to that of the LSG at JSC in the form of a crude glovebox and then test the device itself inside that glovebox. Once the glovebox is created, the team will conduct the remaining validation procedures to ensure that the device meets all the specifications. The team will conduct a pressure test using a vacuum pressure gauge to ensure that the glove mechanism remains sealed and maintains the LSG pressure vacuum. The next validations remaining are the evacuation time, the glove displacement, and unfastening cycles. The team plans to conduct approximately 30 trials to test the evacuation time and approximately 100 trials to check the inner grooves by fastening/unfastening the mechanism. Lastly, the team plans on conducting three 5-minute trials on three different hand sizes to measure the glove displacement after using the gloves for 5 minutes.
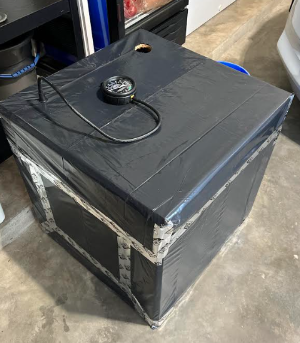
Comments