The Glove Mechanism Physical Prototype
- John Parani
- Feb 18, 2023
- 3 min read
Inner and outer enclosures have been fully printed, with the o-ring installed in the outer enclosure and vacuum grease applied to aid in lubrication and seal, allowing for the entire prototype to be completed and assembled. Both enclosures with the involvement of the o-ring are confirmed to fit together. Initially, the inner enclosure utilized a lip to hold the glove onto the device. This has been omitted in favor of a worm gear clamp. The worm gear clamp is surrounded by heat shrink to protect the glove from its sharp edges and a winged socket has been attached for ease of tightening the clamp without the use of a screwdriver. This worm gear clamp mechanism will also be applied onto the outer enclosure to fasten the hypalon sleeve to the device. In addition to omitting the lip, the inner enclosure has been further extruded to ensure that it will be in contact with the o-ring at all settings with the new fastening method.

O-ring seal installed and lubricated with vacuum grease
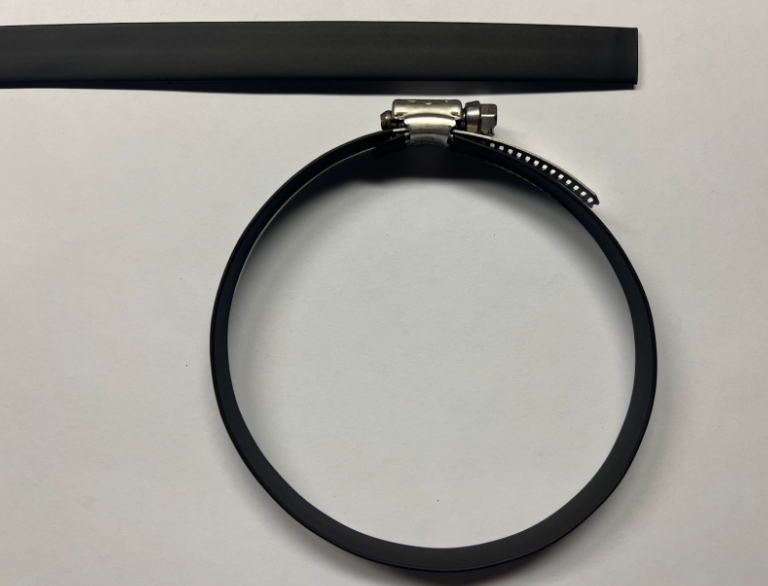
Worm gear wrapped in heat shrink

Wind modification for worm gear bolt
With the addition of the worm gear clamp mechanism, new design analysis has been added to the project. Force analysis for glove retention and leak rate analysis for vacuum seal have been performed, resulting in a force of around 355 pounds to displace the glove from the retention of the worm gear clamp. The leak rate analysis resulted in a very minimal leak rate of 4.6964E-8 L/m. Leak rate analysis has also been conducted on a secondary worm gear clamp to be used for validation purposes. This clamp will retain the sleeve to the device in efforts of not permanently bonding the sleeve to the prototype. This result of the analysis also shows a minimal leak rate of 2.778E-8 L/m.
Validation materials have been acquired for upcoming testing at the LSG mockup. The team has acquired a vacuum pressure gauge with a resolution of 1 cmHg, and a digital caliper with a resolution of 0.02 mm. For the validation plan, the team plans to measure o-ring wear by measuring the change in pressure before and after use in the LSG. For the wear on the device, the notches and grooves will be measured to determine if significant wear is experienced through normal use cycles.
With the addition of the worm gear clamp, and upon the previous meeting with Dr. Chang, the team has decided to rework various parts of their Gantt chart. Airflow validation has then been replaced in favor of the leak rate validation with the worm gear clamp. Tasks involving the worm gear clamp design analysis have been added, as well as a task for developing the winged socket for ease of fastening, which have been completed upon the date of this blog post. Existing tasks have also been completed ahead of projected due dates, with a few tasks being finalized, such as prototype reworks and documents. In addition to the Gantt chart rework, a bill of materials has been developed and completed.
Vacuum pressure measurement remains a challenge for two reasons. The vacuum pressure gauge sourced by the team may not have a small enough resolution (1 cmHg) for the small changes in vacuum pressure. The team estimates the LSG to operate at around 25 cmHg and at this pressure, small changes may not be evident considering a very minimal leak rate is expected from design analysis. The second challenge with vacuum pressure measurement is implementing the pressure gauge into the LSG. Team JAMS has inquired about using one of the two MTL (water) connections onboard the LSG to connect the pressure gauge to, however, the team was denied access. If no connection is available to the team as observed in our next visit, Team JAMS will likely utilize a smaller glove port on the side of the LSG to 3D print an interface for the pressure gauge for the purpose of validation.
According to the Gantt chart that has been developed, the next plans for the upcoming period of February 19 to February 25 is to implement further updates to the prototype that seem fitting for the functionality of the device and to update relevant documents accordingly, such as the bill of materials, CAD files, and budget. Within this time period, the team will prepare to test the prototype at the LSG mockup following this time period, on February 27th. During our progress meeting with Dr. Chang, she had mentioned the use of digital pressure gauges as well as the force gauges that can be accessed through University of Houston. In the next couple of days, the team plans on getting in touch with Dr. Chang to use these tools to future examine the mechanism. Afterwards, the team will source the materials and manufacturing of the final design.
Comments