The Validation Results for our Glove Mechanism
- John Parani
- Apr 15, 2023
- 3 min read
JAMS has completed all the validation that was planned, despite setbacks with NASA bumping the team off of NASA’s schedule. The team reworked all validation and created a glovebox environment that fit our needs. Our LSG mock-up was created using a 24” x 24” x 24” wooden box with plastic covering and a release valve to simulate the slight vacuum on the real LSG. The pressure intended for our validation was 20 cmHg, but we had to settle for 10 cmHg with our mock-up. This change made our pressure measurement less conclusive, but still resulted in 1 cmHg pressure change which fit within our validation.
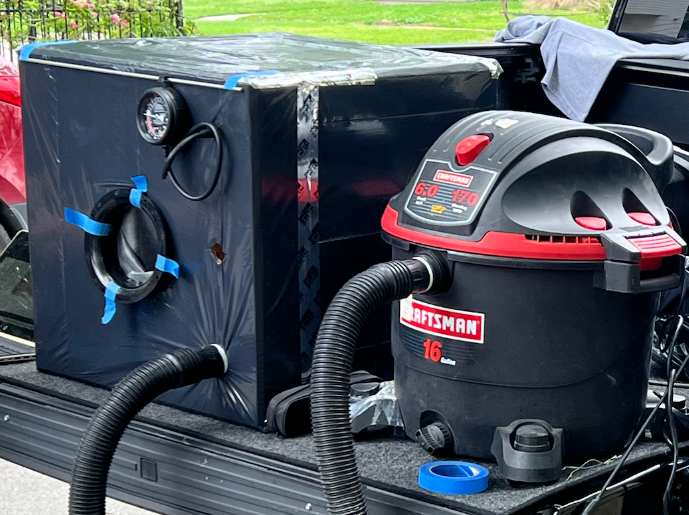
Figure I: Mock-up LSG made by Team JAMS.
All the projected validation was completed on the mock-up LSG including pressure difference of no more than 1 cmHg while using the glove mechanism, evacuation time of minimum 12 seconds, gloves displaced no more than 5 mm after at least a 5 minute period of use, and 100 fastening cycles with no wear of 0.2 mm to the notches/grooves along with 0 cmHg pressure change after fastening cycles. Additionally, device circumference was validated above 10 inches at 13.8 inches. The validation results along with the projected goals are listed further in the blogpost.
The team also completed additional validation using the Experimental Methods force gauge. We measured the forces applied on the device as well as the sleeve, concluding that the average force on the sleeve is 5.85 lbs and the average force on the device 4.4 lbs. These forces are significantly lower than the force required to cause deformation on either the sleeves or plastic of the glove mechanism.
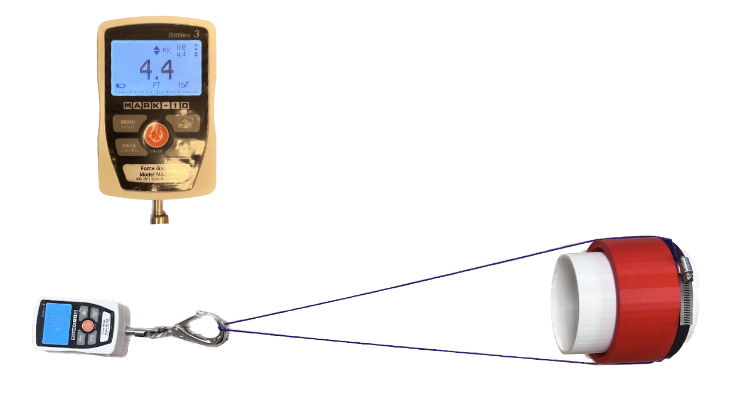
Figure II: Force on Device Procedure with Force Gauge Reading.
The team was recommended by Dr. Chang to further validate the pressure reading by measuring the pressure on the mock-up LSG with the gloveport covered to see if any of the pressure loss is from the sleeves. Our LSG mock-up used sandblasting gloves as sleeves instead of hypalon sleeves which are used on the real LSG. This validation data point could result in more conclusive evidence that our device doesn’t cause a majority of the pressure loss and that the pressure is lost in the DIY sleeves. Therefore, the team has completed all validation, but will need to reconvene for one final validation.

Figure III: Glove and Sleeve Assembly with Sandblasting Sleeves.
The only other deliverable that the team must still complete before the final technical report is a User Manual, which should be done before the poster deadline. Otherwise, all deliverables and goals have been met, and all projected validation has been completed along with bonus validation.
The current validation results support the team’s design in all aspects except one, the pressure difference. The pressure gauge used by the team had a relatively low resolution resulting in the validation not being completely conclusive. The team learned that the original validation value of 5% at 20 cmHg will not be met due to device leak rate increasing exponentially with vacuum pressure. Nonetheless, the team was able to successfully execute all other tests and prove that the design reached all set goals.
Table I. Validation Goals and Results.

The above table displays the design’s key validation results and how the team was able to deduce that their solution was successful indeed. The design performed significantly well in all testing, especially the evacuation time. The design could’ve been tested better with the proper pressure gauge testing; however, overall the results were exceptional.
PDF of Technical Poster Below.
Comments