The T-Channel and Preliminary Changes to the LSG Glove Mechanism
- John Parani
- Feb 4, 2023
- 4 min read
The team has 3D printed a section of the channel of the device that the O-ring seal will fit in. It was found that the O-ring seal fits almost perfectly into the channel, and due to the channel being a T-slot, the seal is secured in place, preventing the seal from being broken during use in the LSG. The t-slot also functions to keep the O-ring attached to the outer enclosure of the device as it will be subjected to compression forces and friction from the inner enclosure being moved within the outer enclosure to adjust for sizing. Taking into account that the 3D model of the outer enclosure will likely be printed as one piece, Team JAMS ensured that the seal is able to be placed into the channel as opposed to being slid into the channel. The seal will be coated in vacuum grease that will serve the purpose of both eliminating the permeation of air through the material of the seal while also providing lubrication for the inner enclosure to slide against the outer enclosure.

Sample print of T-slot for O-ring seal fitment
JAMS also finalized a decision for fabrication of the prototype glove device. After consultation with iSolids, the team has determined the proper settings including the required 100% infill and a more precise 0.1 mm layer height for the selected ABS material, a cheaper alternative to the original PEEK plastic selected. The expected cost with ABS is $60, which is a major improvement to the budget since PEEK was almost 20 times more expensive.
As of Team JAMS’s last presentation, advice was received regarding adding a mechanism that will function to keep the nitrile glove secured to the inner enclosure of the device. Currently, the device contains a lip to retain the nitrile glove, however the method can be improved to provide better retention and sealability. Team JAMS is currently researching alternative methods and has so far experimented lightly with removable cable ties. The method is attractive to Team JAMS considering the cable ties are easily replaceable and cost effective similar to the nitrile gloves. These cable ties work similar to regular cable ties but feature a lever that allows them to be removed as easily as they are applied. If the team selects this option, the lip currently used in the device will be replaced with a channel for the retention device to sit in. Team JAMS is also considering design analysis on this retention device to better determine its ability to retain the gloves and provide a vacuum seal. The vacuum seal design analysis will likely be very similar to that of the o-ring seal seen above.
Clamping devices were considered, but the team wanted to avoid clunky designs and avoid adding elastic materials like springs or bands that are more prone to requiring maintenance. Elastic materials also add an additional mode of failure which requires more intensive analysis that may not be feasible this late into the project.
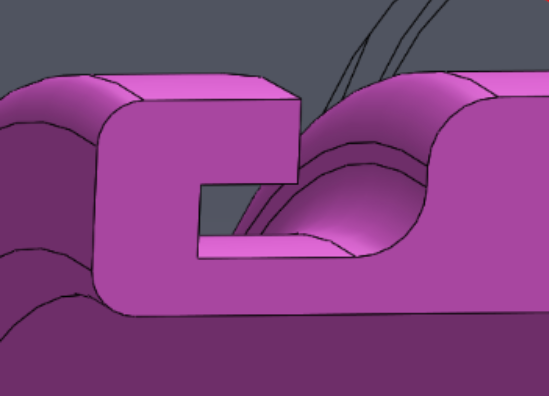
Current lip used in the device to retain the nitrile glove

Removable cable ties
Upon successful testing of the channel and seal, the team was also considering the use of a reusable zip tie to ensure that the gloves stays on and ensuring vacuum seal. However, if a zip tie is used, the user should understand the intended design of the zip tie on the device.
After meeting with Dr. Chang for an instructor update meeting, it became apparent that there are many challenges that will occur during the testing period, with the validation plan being the largest concern, requiring more details. The team was told that they would need a barometer with a proper resolution or even a different tool for validation of pressure difference, as it may be difficult to accurately measure pressure change in the mock-up LSG. The team had also stated that they were performing 30 data points, in which they should be able to report back device damage and wear in measurable and quantifiable results. This challenge may be able to be solved by measuring wear in the device’s notches by measuring width before and after testing, as well as determining wear from loss of pressure or leaks in the device. For testing and ensuring seal after wear cycles, it may be possible to run tests under vacuum to see if performance has changed. For testing displacement, the current validation plan is to measure initial and final hole size in the gloves to determine displacement, which is not an accurate measure of wear, as it is only an initial and final result. This may be fixed by measuring between time intervals and actions performed during testing. However, the results from these may still be taken with a grain of salt, and may not be very viable for determining displacement.
As for the upcoming testing period, the team was told that the testing may take a very long time, and that having it all performed in a single day at the mock-up LSG may not be viable, as in the case of a validation failure, the design may have to be reworked appropriately. The team is considering leaving time to create secondary prints if necessary, and setting multiple dates for testing stages, with each stage focusing on separate parameters and minor reworks that may be necessary.
JAMS’s next steps involve trying to find a solutions to all the concerns that were brought up by Dr. Chang. The team also plans on meeting with Dr. Love again to regain a better understanding on what measurement tools to use and how the team should conduct the validation plans. The team lacks a complete understanding on how to showcase the validation of the device and what to account for, hence proper research and guidance by Dr. Love will help the team enhance the device as well as the testing process. The team plans to have at least one prototype complete so that it could be tested. Because one of the main constraints at the moment is time, the team needs to start testing and the validation plan by the end of February.
Comments